امروزه در شاتل های فضایی، هواپیماهای تجاری، زیر لایه های الکترونیکی (زیر لایه هایی هستند که اجزای مدارهای الکتریکی نظیر ترانزیستورها یا تقویت کننده ها و یکسو کننده های جریان الکتریکی، دیود ها و مدارهای مجتمع یا آی سی ها روی آنها لایه گذاری می شوند و به نام ویفر شناخته می گردند) و در دوچرخه ها، خودروها، چوب گلف و در بسیاری کاربردهای متنوع دیگر، کامپوزیت های زمینه فلزی به طور آزمایشی استفاده شده است. با وجودیکه کامپوزیت های زمینه آلومینیومی قسمت اعظم کامپوزیت های زمینه فلزی را تشکیل می دهند اما در برخی کاربردهای جدید به خواص مکانیکی نیاز است که ابرآلیاژها، تیتانیم، مس، منیزیم یا آهن از آن خواص برخوردار می باشند. بنابراین در کاربردهای مذکور باید از این فلزات به عنوان ماده زمینه کامپوزیت ها استفاده نمود. لازم به ذکر است که ابرآلیاژ ها در دماهای بالا مورد استفاده قرار می گیرند و نسبت به خوردگی و ساییدگی مقاوم می باشند. ضمناً در آلیاژهای مذکور از عناصر آهن، نیکل، کبالت، کروم، تنگستن، مولیبدن و تیتانیم استفاده می گردد.
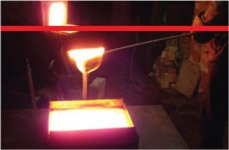
کامپوزیت های زمینه آلومینیومی نیز نظیر دیگر کامپوزیت ها از چند جزء ساخته شده اند و سفتی، استحکام، چگالی و رسانایی حرارتی و الکتریکی مواد تشکیل دهنده آنها قابل اصلاح است. به عبارت دیگر در کامپوزیت های زمینه فلزی برای دسترسی به خواص مطلوب می توان آلیاژ زمینه، مواد تقویت کننده، حجم و شکل تقویت کننده، محل تقویت کننده و روش تولید را تغییر داد.
بین کامپوزیت های زمینه آلومینیومی و دیگر کامپوزیت های زمینه فلزی تفاوت هایی وجود دارد اما پایین بودن قیمت کامپوزیت های زمینه آلومینیومی یکی از مزایای مهمی است که بیشتر کامپوزیت های زمینه فلزی از آن بی بهره می باشند. رسانایی حرارتی بالا، استحکام برشی بالا، مقاومت بالا در برابر سایش، دمای عملکرد بالا، غیر قابل اشتعال بودن، خوردگی پایین در مجاورت سوخت و حلال و امکان تولید و فرآوری با تجهیزات و فناوری های رایج از دیگر مزایای کامپوزیت های زمینه آلومینیومی می باشد. کامپوزیت های زمینه آلومینیمی با فرآیند ریخته گری، متالوژی پودر، تقویت کردن به روش درجا و پرس گرم لایه های فویل/ الیاف تولید می گردند. لازم به ذکر است که روش درجا یکی از روشهای جدید ریخته گری است که در آن تقویت کننده در داخل مذاب تولید می شود. در حقیقیت بین فلز مذاب و ماده ای که به آن اضافه شده است، واکنش شیمیایی صورت می گیرد که به تقویت فلز فاز زمینه منجر می گردد.
در حال حاضر تولید کنندگان بزرگی وجود دارند که کامپوزیت های زمینه فلزی را به طور انبوه، با کیفیت بالا و با قیمت پایین در اختیار مصرف کنندگان قرار می دهند. تولید کنندگان مذکور در دیسک ترمز، پیستون و دیگر قطعات خودرو از کامپوزیت های زمینه فلزی استفاده می کنند. به علاوه تولید کنندگانی نیز وجود دارند که در چوب گلف، دوچرخه، قطعات ماشین آلات، در زوایا و شیارهای قطعات اکسترود شده، زیرلایه های الکترونیکی و در کاربردها و سازه های الکترونیکی دیگر از کامپوزیت های زمینه فلزی استفاده می کنند.
در موتور جت ها قطعاتی وجود دارند که در دمای بالاتر از 1000 درجه سانتی گراد کار می کنند. بنابراین کامپوزیت های زمینه ابرآلیاژ تقویت شده با الیاف تنگستن در قطعات مذکور از خود کارایی بالایی نشان می دهند. در صنایع هوافضا نیز از خواص اصلاح شده کامپوزیت های مس-کربن بهره برده می شود. کامپوزیت های مذکور از خواص مکانیکی و رسانایی الکتریکی و حرارتی بالایی برخوردار می باشند.
شکل دهی کامپوزیت های مس-کربن از کامپوزیت تیتانیوم راحت تر است و چگالی آنها از فولاد کمتر می باشد. ماده زمینه کامپوزیت های ابر رسانای چکش خوار، از مس است و تقویت کننده آنها نیز الیاف نیوبیم-تیتانیم می باشد.
در هیت سینک کامپیوتر ها (خنک کننده قطعات سخت افزاری) و در بسته بندی قطعات الکترونیکی نیز از کامپوزیت های زمینه مس تقویت شده با ذرات تنگستن یا ذرات اکسید آلومینیوم استفاده می گردد. در حال حاضر نیز برای هواپیماهای سازمان ناسا، پوسته ای از جنس کامپوزیت زمینه تیتانیم تقویت شده با الیاف سیلیکون کاربید در دست تولید است.
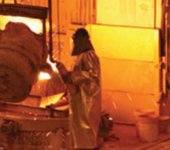
در کمپرسور موتور جت ها (که هوا را متراکم می کند تا به سمت محفظه احتراق برود) و در سایر قطعاتی که باید در برابر دمای بالا و خوردگی از مقاومت بالایی برخوردار باشند، از فولاد ضد زنگ، فولاد ابزار و اینکونل به عنوان ماده زمینه کامپوزیتهای تقویت شده با ذرات کاربید تیتانیم استفاده می گردد. لازم به ذکر است که اینکونل یک ابرآلیاژ پایه نیکل می باشد و در دماهای بالا مورد استفاده قرار می گیرد.
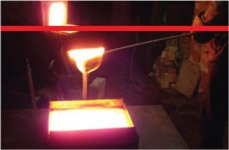
کامپوزیت های زمینه آلومینیومی نیز نظیر دیگر کامپوزیت ها از چند جزء ساخته شده اند و سفتی، استحکام، چگالی و رسانایی حرارتی و الکتریکی مواد تشکیل دهنده آنها قابل اصلاح است. به عبارت دیگر در کامپوزیت های زمینه فلزی برای دسترسی به خواص مطلوب می توان آلیاژ زمینه، مواد تقویت کننده، حجم و شکل تقویت کننده، محل تقویت کننده و روش تولید را تغییر داد.
بین کامپوزیت های زمینه آلومینیومی و دیگر کامپوزیت های زمینه فلزی تفاوت هایی وجود دارد اما پایین بودن قیمت کامپوزیت های زمینه آلومینیومی یکی از مزایای مهمی است که بیشتر کامپوزیت های زمینه فلزی از آن بی بهره می باشند. رسانایی حرارتی بالا، استحکام برشی بالا، مقاومت بالا در برابر سایش، دمای عملکرد بالا، غیر قابل اشتعال بودن، خوردگی پایین در مجاورت سوخت و حلال و امکان تولید و فرآوری با تجهیزات و فناوری های رایج از دیگر مزایای کامپوزیت های زمینه آلومینیومی می باشد. کامپوزیت های زمینه آلومینیمی با فرآیند ریخته گری، متالوژی پودر، تقویت کردن به روش درجا و پرس گرم لایه های فویل/ الیاف تولید می گردند. لازم به ذکر است که روش درجا یکی از روشهای جدید ریخته گری است که در آن تقویت کننده در داخل مذاب تولید می شود. در حقیقیت بین فلز مذاب و ماده ای که به آن اضافه شده است، واکنش شیمیایی صورت می گیرد که به تقویت فلز فاز زمینه منجر می گردد.
در حال حاضر تولید کنندگان بزرگی وجود دارند که کامپوزیت های زمینه فلزی را به طور انبوه، با کیفیت بالا و با قیمت پایین در اختیار مصرف کنندگان قرار می دهند. تولید کنندگان مذکور در دیسک ترمز، پیستون و دیگر قطعات خودرو از کامپوزیت های زمینه فلزی استفاده می کنند. به علاوه تولید کنندگانی نیز وجود دارند که در چوب گلف، دوچرخه، قطعات ماشین آلات، در زوایا و شیارهای قطعات اکسترود شده، زیرلایه های الکترونیکی و در کاربردها و سازه های الکترونیکی دیگر از کامپوزیت های زمینه فلزی استفاده می کنند.
در موتور جت ها قطعاتی وجود دارند که در دمای بالاتر از 1000 درجه سانتی گراد کار می کنند. بنابراین کامپوزیت های زمینه ابرآلیاژ تقویت شده با الیاف تنگستن در قطعات مذکور از خود کارایی بالایی نشان می دهند. در صنایع هوافضا نیز از خواص اصلاح شده کامپوزیت های مس-کربن بهره برده می شود. کامپوزیت های مذکور از خواص مکانیکی و رسانایی الکتریکی و حرارتی بالایی برخوردار می باشند.
شکل دهی کامپوزیت های مس-کربن از کامپوزیت تیتانیوم راحت تر است و چگالی آنها از فولاد کمتر می باشد. ماده زمینه کامپوزیت های ابر رسانای چکش خوار، از مس است و تقویت کننده آنها نیز الیاف نیوبیم-تیتانیم می باشد.
در هیت سینک کامپیوتر ها (خنک کننده قطعات سخت افزاری) و در بسته بندی قطعات الکترونیکی نیز از کامپوزیت های زمینه مس تقویت شده با ذرات تنگستن یا ذرات اکسید آلومینیوم استفاده می گردد. در حال حاضر نیز برای هواپیماهای سازمان ناسا، پوسته ای از جنس کامپوزیت زمینه تیتانیم تقویت شده با الیاف سیلیکون کاربید در دست تولید است.
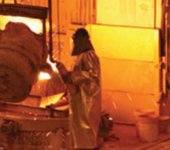
در کمپرسور موتور جت ها (که هوا را متراکم می کند تا به سمت محفظه احتراق برود) و در سایر قطعاتی که باید در برابر دمای بالا و خوردگی از مقاومت بالایی برخوردار باشند، از فولاد ضد زنگ، فولاد ابزار و اینکونل به عنوان ماده زمینه کامپوزیتهای تقویت شده با ذرات کاربید تیتانیم استفاده می گردد. لازم به ذکر است که اینکونل یک ابرآلیاژ پایه نیکل می باشد و در دماهای بالا مورد استفاده قرار می گیرد.